Keeping a Refinery Turnaround on Track in Pascagoula
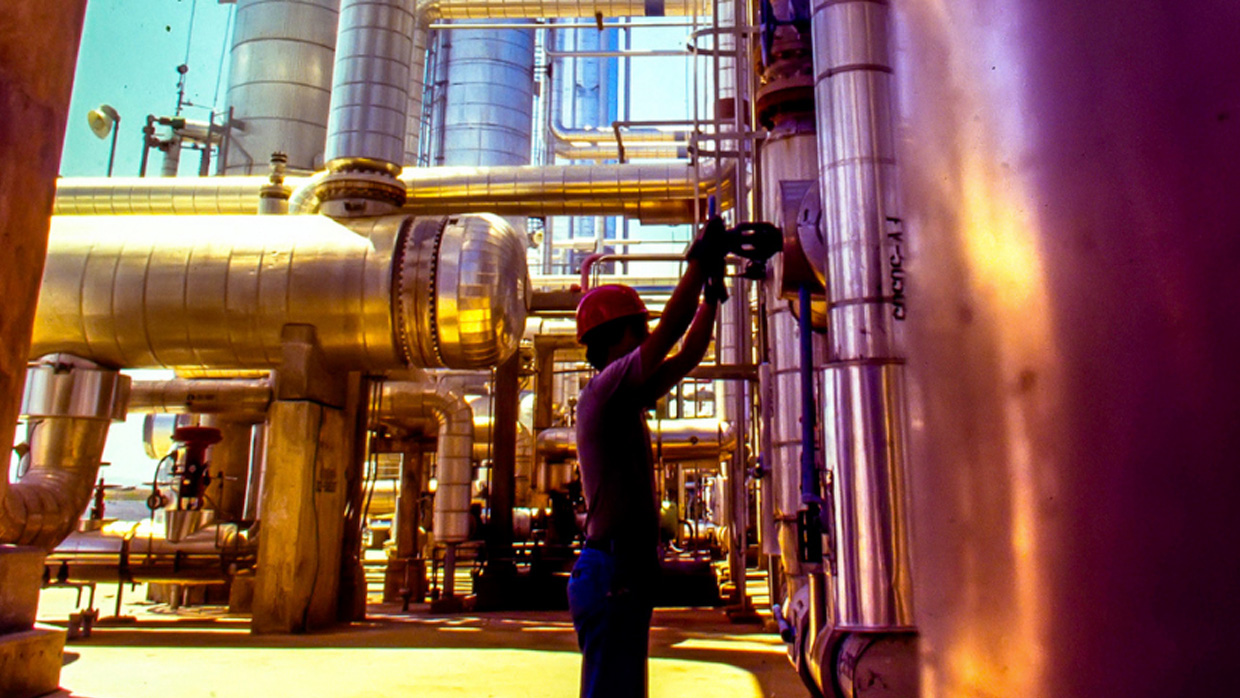
Overview
Our client’s refinery in Pascagoula, Mississippi is the company’s largest and most complex refinery. One of the top petroleum refineries in the United States, it produces an average of 350,000 barrels of petroleum liquids per day. In January 2022, the 6,000-acre refinery slowed down production for a planned major turnaround, the second largest in its 60-year history. Sodexo's on-site presence was beneficial for cost and time savings. Over three months, our team kept the schedule on track by delivering a range of services for an additional 4,800 workers on-site and solving large-scale logistical projects.
At this refinery turnaround, Sodexo played a key role in supporting our client with many aspects of the large-scale project including catering and sanitation services, logistical support, and supplies and materials acquisition. In addition, our team was tasked with removing and reinstalling security gate equipment to facilitate transportation and deliveries of oversized equipment.
Sodexo has been providing facilities management to this site since 2019. This turnaround was the first project of its scale at the site that our team worked on.
By the Numbers
- 24/7 operations uninterrupted for 11 weeks
- 6,000-acre refinery site
- Up to 4,800 additional contractors on site
- 65 Sodexo employees
Objectives
With up to 4,800 additional workers on-site, the Sodexo team in Pascagoula had their work cut out for them. Some challenges included:
- Providing janitorial and cleaning services for double the workforce on-site
- Provided internal catering to a total of 13,537 guests in a three-month period, as well as assisting the refinery in facilitating external caterers to prepare 2,000 meals/day
- Installing three different lunch tents with a total of 1,200 seats
- Acquiring and installing 120 microwaves
- Supplying and installing furniture for 25 modular office units
- Providing the audio system in the control tent
- Facilitating and managing the inventory for 18 vending machines, triple the usual inventory at this site
- Supplying and servicing 50% more portable restrooms than are on-site during normal operations
- Coordinating the transportation logistics of a 2,500-ton crane brought in for a half-ton module assembly
Our Solution-Oriented Approach
Despite the nationwide supply chain disruptions that have been an endemic component of business since 2020, our team rose to the challenge and provided uninterrupted support without compromising service excellence.
One of the main factors in the team's success was being part of the planning meetings from the start. The team understood the scope of needs and planned accordingly, especially in anticipating supply chain disruptions. Due to Sodexo’s proactivity, despite delays in deliveries and unusually high numbers in some supplies, the team was ready and operational on January 10, the start date of the turnaround.
Leveraging Sodexo’s Supply Management
When one of Sodexo’s vendors ran out of a product requested by our client, our team stepped in and built the missing inventory themselves, tailored specifically to the project.
To cover all needs throughout the 11-week project, the Sodexo team worked a combined 1,400 hours – almost two months' worth of hours - more than normal operations require across all departments. Most of these hours were provided by the janitorial team, who went from working five days a week to seven to provide a sanitary environment for all the additional personnel on-site.
Tackling a Special Project with Expertise
To successfully assemble the half-ton module our team needed to seriously modify the refinery site’s infrastructure during this period. Far larger than could be brought in by truck, our team disassembled the truck gate to make space for the 2,500-ton crane to be brought in. This feat required us to remove badge readers and security cameras typically in place at the gate. We did this not only once, but three times during the 11-week period, coordinating hundreds of 18-wheelers and the assembly of all their cargo.
Results
Despite the significant challenges faced, our team maintained their daily services for thousands more client employees with no additional staff. Their success in accomplishing this enormous project is a testament to Sodexo’s operational excellence.