Revitalizing Refinery Infrastructure Seamlessly with Sodexo
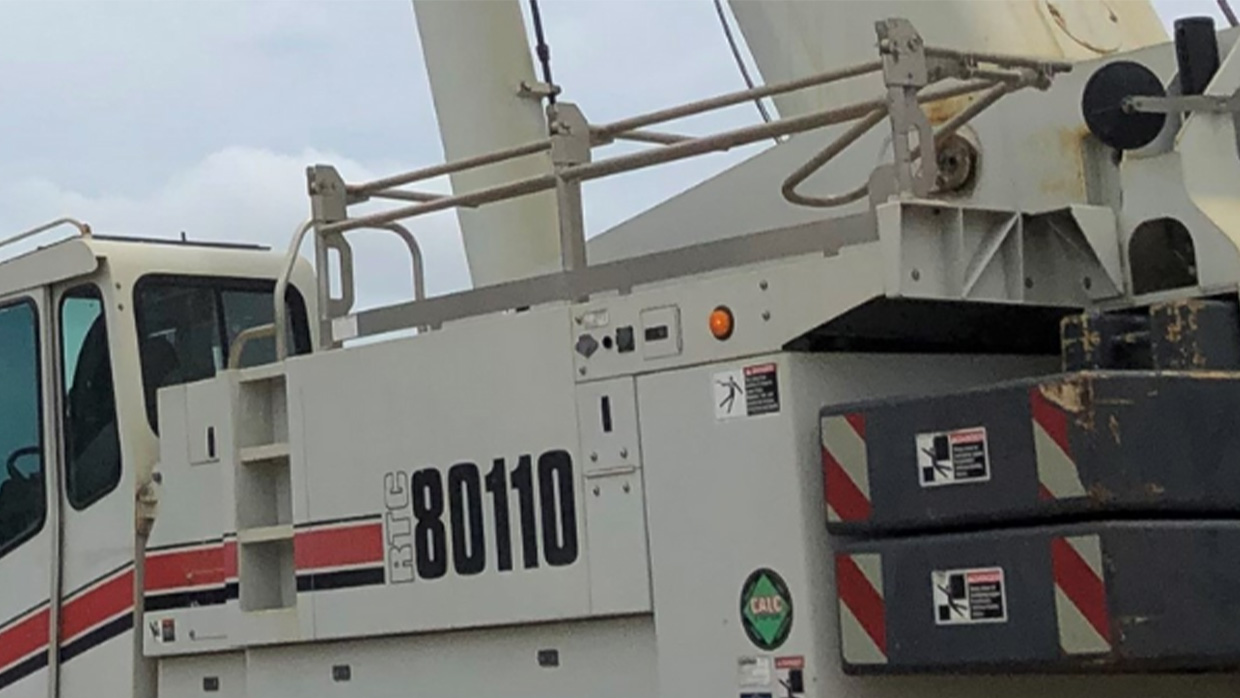
When the winter storm hit Texas in early 2021, many of our client sites sustained considerable damage. Returning operations to their pre-storm conditions came with some challenges.
In addition to our teams mobilizing in the immediate aftermath of the storm, our operators proactively problem-solved by developing and executing a solution when the aging chiller at one of our global client’s large refineries sustained major damage following the freeze.
Finding Solutions Despite Challenges
The goal was to replace the original, 20-year-old, 150-ton external chiller, as well as coils on the internal air handling, without disrupting operations.
Since uncontrolled fluctuations above or below the designated temperature threshold could significantly alter test results for oil and gas sampling, the only available options were to provide supplemental cooling while awaiting delivery of the new equipment by providing two portable rental units. Due to the supply backlog impacted by the freeze, this temporary measure was in place for five months.
Our project management team worked diligently with the client to assess needs and coordinate the logistics of equipment purchase and installation on site. Once the unit arrived, our service operations team worked with the vendors for start-up validation, technician training and deployment into the asset management system.
Asserting Reliability and Trust
Replacing the aging and damaged chiller provided a stable environmental platform for testing purposes and, most importantly, brings long-term energy and cost savings. This unit also provides comfort cooling for the office areas, improving working conditions for employees in the summer months.
Having the system back up and operational thanks to the excellent work of our dedicated operators attests to the reliability of our teams to proactively problem-solve and to provide ongoing support and services.
Our clients know they can trust us because we empower our frontline teams to be their day-to-day partners — anticipating and responding to their needs, solving their challenges and improving our support to them every day.
Learn more about how you can strengthen resilience in your plant operations.